Advanced High-Strength Steel
Advanced High-Strength Steels are uniquely light weight and are made to meet the expectations of the automotive industry to increase safety, reduce emissions, and increase performance at lower costs.
The SKD team has successfully built numerous number of dies that run AHSS material, from 590MPa to 1180Mpa. Our staff is very experienced in analyzing formability and compensating for springback with AHSS material. With thorough understanding of the fundamental behaviors of high strength steel, we can fine-tune tooling to 100% part conformance with minimum number of quality loops.
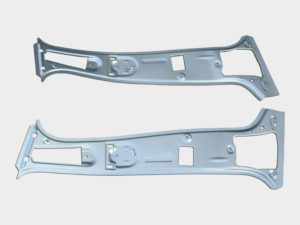
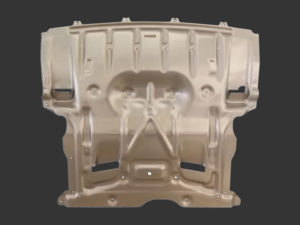
Aluminum Alloys
Due to its lightweight nature, the application of aluminum alloy in automotive parts manufacturing has become a norm for carmakers to replace parts made out of steel alloy to improve fuel efficiency. Mechanical properties of aluminum sheet metal reacts very differently than steel in metal stamping. SKD has much expertise and experience building dies for aluminum sheet metal. Image shown is an aluminum-magnesium alloy skid plate made from a mechanical transfer die that SKD built for BMW.
Aluminum Heat Shields
SKD manufactures dies that allow OEMs to produce automotive heat shields that are lightweight and thermal-insulating. These heat shields are made of heat resistance material laminated with aluminum sheet metal. SKD has the expertise to form such specialty material into various part configurations and satisfy customers’ specific requirements.
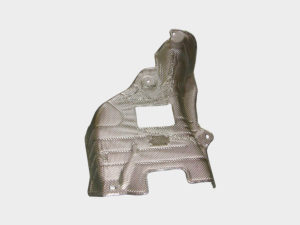
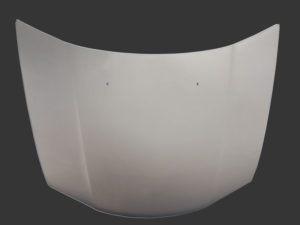
Class A Skin Panels
SKD also produces dies that satisfy OEMs’ Class A surface requirements for Body-In-White assemblies. These Class A parts make up the “exterior skin” of the vehicle. This includes body sides, hoods, doors, roofs and fenders which form the outside appearance of the vehicle and often end up being the largest stampings in the production.
It takes a different kind of tool & die skill set to build dies for exposed Class A components as opposed to unexposed Class C parts. The SKD team has this distinctive expertise and has built many Class A panel dies and has been shipping directly to OEM carmakers such as General Motors and Honda for over a decade.
Tailor Rolled Blanks
Tailor Rolled Blank is a semi-finished sheet metal product that is used to further produce different stamping parts that have a continuous wide range of material thickness variations. Due to the variation in material thickness within one sheet metal, material flow inside a forming or draw die requires precise analysis to predict formability and springback as well as the location of material thickness transitions in the final part. Example shown is a crossmember component made from a die SKD built directly for OPEL in Germany. This component is made out of Tailor-Rolled Blanks with five different material thicknesses. SKD successfully completed fine-tuning the die with 100% part quality in just one quality loop.
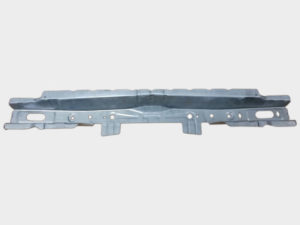
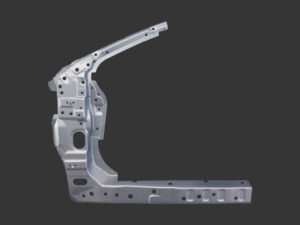
Tailor Welded Blanks
Tailor Welded Blanks, much like tailor rolled blanks, are made from individual steel sheets of different thickness, strength and coating which are joined together by laser welding – allowing for more flexible component design and at the same time reducing vehicle weight by eliminating overlapping material for joining different materials.
The image shown is a component made out of a Tailor Welded Blanks that combines an A-Pillar and a Rocker Panel. This joined component has two different high strength materials with two different thicknesses. SKD built this die with 100% part tolerance accuracy, including location of laser weld line, for Mitsubishi Motors from design to first sample in just 10 weeks.